Calcula el tiempo estándar de forma rápida y precisa con estos consejos expertos sobre cómo hacerlo
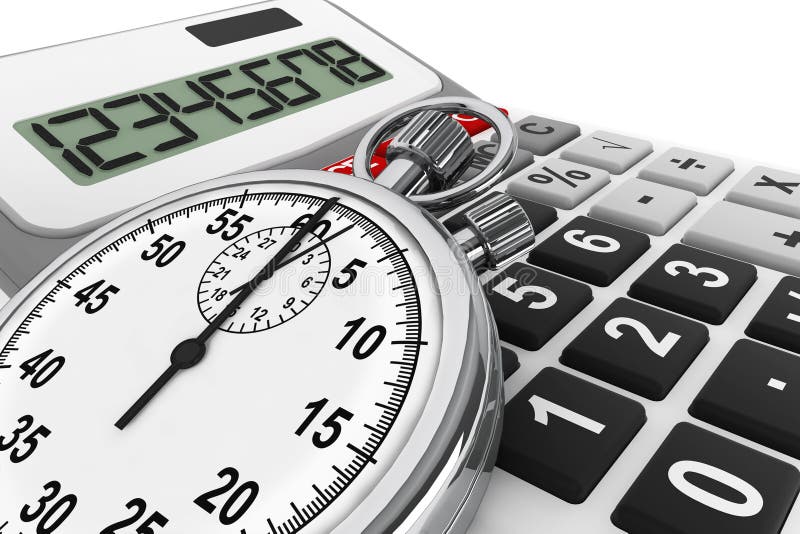
El cálculo del tiempo estándar es un proceso esencial en los procesos de producción y fabricación. Ya sea que estés desarrollando un producto nuevo o mejorando las operaciones existentes, el tiempo estándar te permite tener una estimación precisa de cuánto tiempo tomará completar una tarea.
Te presentaremos algunos consejos expertos sobre cómo calcular el tiempo estándar de forma rápida y precisa. Analizaremos los factores clave que debes considerar, como el método de medición, la experiencia del trabajador, las condiciones del entorno y más. También te proporcionaremos algunas herramientas y técnicas útiles para hacer el cálculo más eficiente y confiable. Aprender a calcular adecuadamente el tiempo estándar puede ayudarte a mejorar la planificación, optimizar la eficiencia y maximizar la productividad en tus operaciones.
- Cuáles son los beneficios de calcular el tiempo estándar en la producción
- Cómo se calcula el tiempo estándar en un proceso de producción
- Qué factores se deben tener en cuenta al calcular el tiempo estándar
- Cuáles son las técnicas más eficientes para medir el tiempo estándar en la producción
- Cómo se pueden optimizar los métodos de medición del tiempo estándar
- Cuál es la importancia de realizar un seguimiento continuo del tiempo estándar en la producción
- Qué herramientas tecnológicas existen para ayudar en el cálculo del tiempo estándar
- Cuáles son los errores comunes que se deben evitar al calcular el tiempo estándar
- Cómo se puede establecer un sistema efectivo de registro y análisis del tiempo estándar en la producción
- Qué consejos prácticos pueden ayudar a mejorar la precisión en el cálculo del tiempo estándar
- Preguntas frecuentes (FAQ)
Cuáles son los beneficios de calcular el tiempo estándar en la producción
Calcular el tiempo estándar en la producción es una práctica esencial para cualquier empresa que busque optimizar sus procesos y mejorar su eficiencia. Esta técnica permite determinar cuánto tiempo se tarda en realizar una actividad o llevar a cabo un proceso específico, lo que resulta increíblemente útil para planificar la capacidad de producción, establecer tiempos de entrega realistas y evaluar la productividad del personal.
Uno de los principales beneficios de calcular el tiempo estándar es que ayuda a identificar oportunidades de mejora continua. Al conocer cuánto tiempo se tarda en completar una tarea, es posible analizar cada paso del proceso y encontrar áreas donde se puede reducir el tiempo o aumentar la eficiencia. Esto puede incluir la eliminación de pasos innecesarios, la automatización de ciertas tareas o la optimización de la secuencia de trabajo.
Otro beneficio importante es la capacidad de establecer estándares de desempeño claros y medibles. Al calcular el tiempo estándar, se obtiene un punto de referencia objetivo que se puede utilizar para evaluar el desempeño de los empleados. Esto permite identificar rápidamente a aquellos que están por debajo del estándar y brindarles el entrenamiento adicional necesario para mejorar su rendimiento.
Además, calcular el tiempo estándar también ayuda a gestionar de manera más efectiva la carga de trabajo y asignar los recursos adecuados. Conociendo el tiempo que toma completar cada tarea, es posible programar las actividades de manera óptima, evitando retrasos y desperdicio de recursos. Esto también permite una distribución equitativa de la carga de trabajo, evitando que algunos empleados se vean sobrecargados mientras que otros tienen una carga más ligera.
Por último, calcular el tiempo estándar también contribuye a mejorar la planificación y estimación de costos. Al conocer el tiempo requerido para completar una tarea, es posible realizar proyecciones más precisas sobre la duración total de un proyecto y los recursos necesarios. Esto ayuda a evitar retrasos en la entrega, ajustes de presupuesto y otros problemas relacionados con la gestión inadecuada del tiempo.
Cómo se calcula el tiempo estándar en un proceso de producción
El cálculo del tiempo estándar es una parte fundamental en la gestión eficiente de cualquier proceso de producción. Se refiere al tiempo necesario para que un operario cualificado realice una tarea específica siguiendo los métodos y condiciones establecidos. Este cálculo es esencial para determinar la capacidad productiva de una empresa, programar la producción de manera efectiva y hacer estimaciones precisas sobre el tiempo requerido para realizar diferentes tareas.
Para calcular el tiempo estándar, es importante seguir una metodología adecuada y utilizar herramientas y técnicas confiables. Aquí te presentamos algunos consejos expertos sobre cómo hacerlo de manera rápida y precisa:
1. Observación directa
Una forma común de calcular el tiempo estándar es mediante la observación directa de un operario realizando la tarea. Durante esta observación, se debe registrar el tiempo que toma cada paso o actividad dentro del proceso de producción. Es importante tener en cuenta factores como la fatiga del trabajador, posibles interrupciones y tiempos muertos. Esta información será la base para realizar el cálculo posteriormente.
2. División del trabajo en elementos cronometrables
Una vez se ha realizado la observación directa, es necesario dividir el trabajo en elementos más pequeños y fáciles de medir. Estos elementos deben ser independientes y estar bien definidos. Por ejemplo, si el proceso de producción implica ensamblar un producto, los elementos pueden ser: tomar la pieza A, unir la pieza B, ajustar los tornillos, entre otros. Al dividir el trabajo en elementos, se facilita el cálculo del tiempo estándar ya que se pueden medir y analizar por separado.
3. Determinación de los tiempos de ciclo
Una vez que se han identificado los elementos de trabajo, es necesario determinar los tiempos de ciclo para cada uno. El tiempo de ciclo se refiere al tiempo promedio que toma realizar un elemento específico del proceso de producción. Esto se puede lograr mediante la repetición de la tarea varias veces y registrando el tiempo que toma en cada ocasión. Al obtener una muestra suficiente, se puede calcular el promedio y utilizar este valor como base para el cálculo del tiempo estándar.
4. Consideración de factores externos e internos
Además de los tiempos de ciclo, es esencial considerar los factores externos e internos que pueden afectar el rendimiento de un operario y el tiempo requerido para realizar una tarea. Los factores externos pueden incluir condiciones ambientales, interrupciones en el flujo de trabajo o problemas de equipamiento. Por otro lado, los factores internos pueden ser las habilidades y capacitación del operario, así como su nivel de experiencia. Es importante tener en cuenta todos estos factores al realizar el cálculo del tiempo estándar para tener estimaciones precisas.
5. Utilización de software especializado
En la actualidad, existen numerosas herramientas y software especializados que facilitan el cálculo del tiempo estándar. Estos programas permiten automatizar el proceso de recopilación y análisis de datos, así como generar informes detallados y precisos. Al utilizar software especializado, se aumenta la eficiencia y se reduce el margen de error en el cálculo del tiempo estándar.
El cálculo del tiempo estándar en un proceso de producción es crucial para una gestión efectiva y eficiente. Sigue estos consejos expertos y utiliza las herramientas adecuadas para lograr estimaciones rápidas y precisas. Recuerda que el tiempo estándar es una medida dinámica que debe actualizarse periódicamente para adaptarse a los cambios en los métodos de trabajo y las condiciones del entorno.
Qué factores se deben tener en cuenta al calcular el tiempo estándar
Al calcular el tiempo estándar, es importante tener en cuenta varios factores para garantizar una estimación precisa y confiable. Estos factores incluyen:
Tareas involucradas
Es fundamental identificar todas las tareas que conforman el proceso o la actividad que se desea medir. Cada tarea debe ser analizada individualmente para determinar su duración y complejidad.
Descomposición del trabajo
Para obtener una estimación precisa, es necesario descomponer cada tarea en sus componentes más pequeños y manejables. Esto facilitará el análisis individual de cada paso y permitirá una mejor comprensión de los tiempos involucrados.
Experiencia previa
La experiencia previa del analista en tareas similares puede ser de gran ayuda al calcular el tiempo estándar. El conocimiento adquirido a través de proyectos anteriores permite realizar estimaciones más precisas y considerar posibles problemas que puedan surgir durante el proceso.
Variabilidad
Es fundamental tener en cuenta la variabilidad inherente a cualquier proceso o tarea. Las fluctuaciones en las condiciones de trabajo, la disponibilidad de recursos, el nivel de habilidad del personal y otros factores pueden influir en la duración del proceso. Se recomienda utilizar datos históricos y estadísticas para tener en cuenta esta variabilidad y así ajustar las estimaciones de tiempo.
Análisis de métodos
El análisis de los métodos utilizados para llevar a cabo las tareas también es esencial al calcular el tiempo estándar. Este análisis implica evaluar la eficiencia de los distintos pasos del proceso y buscar oportunidades de mejora. Al realizar cambios en el método, es posible reducir significativamente el tiempo requerido para completar una tarea.
Capacidad humana
La capacidad física y mental del personal encargado de llevar a cabo las tareas también debe ser considerada al calcular el tiempo estándar. Es importante tener en cuenta los tiempos de descanso necesarios, así como los posibles errores o demoras debido a fatiga o falta de concentración.
Todos estos factores deben ser tenidos en cuenta al calcular el tiempo estándar con el fin de obtener una estimación precisa y confiable. Una estimación precisa permitirá planificar y distribuir eficientemente los recursos, minimizar los tiempos de espera y mejorar la productividad en general.
Cuáles son las técnicas más eficientes para medir el tiempo estándar en la producción
Medir el tiempo estándar en la producción es una tarea crucial para mejorar la eficiencia y productividad de cualquier negocio. Es un proceso que permite determinar cuánto tiempo debería tomar realizar una tarea en condiciones normales, teniendo en cuenta factores como la habilidad del trabajador, las condiciones del entorno de trabajo y los equipos utilizados. Para llevar a cabo esta medición de forma rápida y precisa, se requiere de técnicas efectivas que nos permitan recopilar los datos necesarios y analizarlos de manera adecuada.
Análisis de flujo de trabajo
Una de las técnicas más eficientes para calcular el tiempo estándar es realizar un análisis exhaustivo del flujo de trabajo. Esto implica descomponer la tarea en subprocesos más pequeños y cronometrar cada uno de ellos individualmente. Al dividir la tarea en partes más manejables, es posible identificar posibles cuellos de botella o áreas de mejora. Además, este enfoque permite obtener mediciones más precisas, ya que cada subproceso puede ser analizado con mayor detalle.
Utilización de cronómetros y software especializado
Otra técnica efectiva para calcular el tiempo estándar es utilizar cronómetros y software especializado. Estas herramientas permiten medir el tiempo de ejecución de cada tarea de manera precisa y confiable. Los cronómetros pueden ser utilizados por los propios trabajadores, quienes pueden activarlos al comenzar una tarea y detenerlos al finalizarla. Por otro lado, el software especializado no solo permite medir el tiempo, sino también recopilar y analizar los datos de forma automática, lo que agiliza el proceso y reduce errores humanos.
Observación directa
La observación directa es una técnica clásica pero efectiva para calcular el tiempo estándar. Consiste en observar y registrar el tiempo que toma realizar una tarea determinada. Para obtener mediciones precisas, es importante repetir la observación varias veces y promediar los resultados. Además, es fundamental contar con observadores capacitados que puedan identificar y registrar cada movimiento o acción relevante durante la realización de la tarea.
Estudio de tiempos y movimientos
El estudio de tiempos y movimientos es una técnica ampliamente utilizada en la industria para calcular el tiempo estándar. Consiste en analizar y medir cada uno de los movimientos involucrados en la realización de una tarea, desde agarrar una herramienta hasta colocar una pieza en su lugar. Este enfoque permite identificar movimientos innecesarios o ineficientes, y sugerir mejoras que reduzcan el tiempo de ejecución de la tarea.
Análisis de datos históricos
Por último, el análisis de datos históricos puede ser una técnica útil para calcular el tiempo estándar. Consiste en utilizar registros previos de mediciones de tiempo para estimar el tiempo necesario para completar una tarea. Si se cuenta con una base de datos confiable y actualizada, es posible realizar pronósticos precisos y ahorrar tiempo en mediciones repetidas.
- Descomponer la tarea en subprocesos más pequeños para un análisis más detallado.
- Utilizar cronómetros y software especializado para medir el tiempo de ejecución.
- Realizar observaciones directas y repetirlas varias veces para obtener mediciones precisas.
- Aplicar el estudio de tiempos y movimientos para identificar movimientos ineficientes.
- Utilizar datos históricos para estimar el tiempo estándar en base a registros previos.
Calcular el tiempo estándar de forma rápida y precisa es fundamental para mejorar la eficiencia y productividad en la producción. Estas técnicas eficientes proporcionadas te ayudarán a obtener mediciones más precisas y identificar oportunidades de mejora en tus procesos.
Cómo se pueden optimizar los métodos de medición del tiempo estándar
El tiempo estándar es una medida utilizada en la ingeniería industrial para estimar la cantidad de tiempo que se requiere para llevar a cabo una determinada tarea o proceso. Es esencial tener un cálculo preciso del tiempo estándar para poder planificar eficientemente la producción, asignar recursos y evaluar el desempeño de los trabajadores.
Aunque existen métodos tradicionales para calcular el tiempo estándar, como los estudios de tiempos y movimientos, estos pueden ser tediosos y consumir mucho tiempo. Afortunadamente, hay consejos expertos y herramientas disponibles que pueden ayudarte a calcular el tiempo estándar de forma rápida y precisa. Aquí te presentamos algunos de ellos:
1. Utiliza software especializado en medición del tiempo estándar
En la actualidad, existen numerosos programas informáticos diseñados especialmente para calcular el tiempo estándar de manera eficiente. Estos softwares te permiten realizar análisis de procesos, capturar datos en tiempo real, y generar informes detallados. Al utilizar un software especializado, puedes ahorrar tiempo y obtener resultados más precisos al eliminar errores humanos y agilizar el proceso de medición.
2. Divide el proceso en actividades más pequeñas
Dividir el proceso principal en actividades más pequeñas te permitirá tener un mayor nivel de detalle al calcular el tiempo estándar. Esto es especialmente útil cuando se trata de tareas complejas que involucran múltiples subprocesos. Al desglosar el proceso en pasos más manejables, podrás identificar los puntos críticos y determinar el tiempo requerido para cada actividad individualmente.
3. Utiliza datos históricos
Si tienes información previa sobre el tiempo requerido para realizar ciertas tareas, puedes utilizar esos datos como base para calcular el tiempo estándar en proyectos futuros. Esto es especialmente útil cuando se trata de procesos repetitivos o tareas que se realizan con frecuencia. Analiza los datos históricos, identifica patrones y tendencias, y utiliza esta información para estimar el tiempo estándar de manera más precisa.
4. Considera factores externos
Al calcular el tiempo estándar, ten en cuenta los factores externos que podrían afectar la duración de una tarea. Estos factores podrían incluir interrupciones, descansos programados, problemas de suministro, entre otros. Considerar estos factores te ayudará a ser más realista al estimar el tiempo necesario para completar una tarea y evitará retrasos innecesarios en la planificación y ejecución del proyecto.
5. Actualiza regularmente tus cálculos
El tiempo estándar puede verse afectado por cambios en los procesos, tecnologías o habilidades de los trabajadores. Es importante revisar y actualizar regularmente los cálculos de tiempo estándar para reflejar cualquier cambio que pueda haber ocurrido. Mantén un seguimiento constante del desempeño de tu equipo y realiza ajustes si es necesario para mantener tus estimaciones de tiempo actualizadas y precisas.
Al seguir estos consejos expertos y utilizar las herramientas adecuadas, podrás calcular el tiempo estándar de forma rápida y precisa. Esto te permitirá tomar decisiones más informadas, optimizar la planificación y mejorar los resultados en tus proyectos de ingeniería industrial.
Cuál es la importancia de realizar un seguimiento continuo del tiempo estándar en la producción
El seguimiento continuo del tiempo estándar es fundamental en el ámbito de la producción, ya que permite calcular y establecer de manera precisa el tiempo necesario para completar una tarea o proceso específico. Esto juega un papel clave en distintos aspectos de la gestión y mejora de la productividad.
Un tiempo estándar bien calculado permite a las empresas planificar sus operaciones de manera eficiente, optimizar los recursos y minimizar los costos. Además, se convierte en una herramienta valiosa para establecer metas realistas, evaluar el rendimiento laboral y detectar posibles ineficiencias en los procesos.
Al tener un conocimiento preciso sobre el tiempo estándar de cada actividad, es posible programar adecuadamente la producción, ajustar los tiempos de entrega y evitar retrasos innecesarios. Esto es especialmente importante en sectores como la manufactura, donde los plazos de fabricación y entrega son críticos.
Asimismo, el cálculo del tiempo estándar es esencial para la evaluación de la capacidad productiva de una empresa. Al conocer el tiempo requerido para la realización de cada actividad, es posible determinar si existe un desajuste entre la demanda y la capacidad de producción, lo que permite tomar decisiones informadas para mejorar la eficiencia y maximizar los recursos disponibles.
Otra ventaja del seguimiento continuo del tiempo estándar es la mejora en la calidad del producto final. Al contar con tiempos establecidos y bien definidos, es posible identificar y corregir errores, eliminar actividades innecesarias y reducir desperdicios. Esto contribuye a incrementar la precisión y consistencia de los productos, así como a optimizar los procesos de control de calidad.
Para llevar a cabo el seguimiento del tiempo estándar de forma efectiva, es recomendable utilizar herramientas y metodologías específicas. La observación directa, los estudios de tiempos y movimientos, así como el uso de software especializado, son algunas de las técnicas más comunes utilizadas en la industria.
El seguimiento continuo del tiempo estándar desempeña un papel crucial en la gestión eficiente de la producción. Su correcto cálculo permite optimizar recursos, reducir costos, mejorar la calidad y maximizar la capacidad productiva de una empresa. Por lo tanto, es fundamental contar con los conocimientos y las herramientas necesarias para realizar esta tarea de manera precisa y rápida.
Qué herramientas tecnológicas existen para ayudar en el cálculo del tiempo estándar
El cálculo del tiempo estándar es una parte vital en la gestión de la producción para muchas industrias. Determinar el tiempo que se requerirá para realizar una tarea o proceso específico puede ayudar a planificar adecuadamente los recursos y mejorar la eficiencia en general.
Afortunadamente, en la era moderna de la tecnología, existen herramientas disponibles que pueden facilitar en gran medida este proceso. Estas soluciones tecnológicas no solo ofrecen un cálculo más rápido del tiempo estándar, sino también mayor precisión en los resultados.
Herramienta de cronometraje
Una de las formas más comunes de calcular el tiempo estándar es mediante el uso de una herramienta de cronometraje. Estas herramientas suelen ser dispositivos electrónicos, como relojes especializados o temporizadores digitales, que permiten medir con precisión la duración de un proceso.
Al utilizar una herramienta de cronometraje, los operarios pueden registrar el tiempo necesario para completar una tarea o realizar un proceso en particular. Este método es especialmente útil cuando se trata de tareas repetitivas, ya que permite obtener mediciones precisas y consistentes.
Software de simulación
Otra opción tecnológica para el cálculo del tiempo estándar es el software de simulación. Este tipo de software permite crear modelos virtuales de procesos específicos y simular su ejecución en un entorno controlado.
El software de simulación tiene la capacidad de analizar múltiples variables y factores que pueden influir en el tiempo necesario para completar una tarea. Al ingresar datos sobre el proceso y los recursos disponibles, el software puede generar estimaciones precisas del tiempo estándar requerido.
Análisis de datos históricos
Además de las herramientas tecnológicas mencionadas anteriormente, también es posible utilizar el análisis de datos históricos para calcular el tiempo estándar. Al recopilar y analizar datos sobre proyectos o procesos anteriores, es posible identificar patrones y tendencias que pueden utilizarse para predecir la duración de tareas futuras.
El análisis de datos históricos permite aprovechar la experiencia pasada y utilizarla como base para estimaciones futuras. A través de técnicas estadísticas y algoritmos especializados, este enfoque puede proporcionar resultados precisos y confiables en función de datos reales.
Existen varias herramientas tecnológicas disponibles que pueden ayudar en el cálculo del tiempo estándar. Ya sea a través de herramientas de cronometraje, software de simulación o análisis de datos históricos, estas soluciones ofrecen una forma rápida y precisa de determinar la duración de tareas o procesos. Al utilizar estas herramientas, las empresas pueden optimizar su gestión de la producción y mejorar su eficiencia en general.
Cuáles son los errores comunes que se deben evitar al calcular el tiempo estándar
Calcular el tiempo estándar es una tarea fundamental en diversos campos de la industria. Sin embargo, es común cometer errores que pueden afectar la precisión y rapidez del cálculo. En esta sección, te presentaremos los errores más comunes que debes evitar al calcular el tiempo estándar, junto con consejos expertos sobre cómo evitarlos.
No considerar todas las tareas involucradas
Uno de los errores más frecuentes al calcular el tiempo estándar es no tener en cuenta todas las tareas necesarias para realizar una actividad. Esto puede llevar a subestimar el tiempo requerido, lo que resultaría en una planificación inexacta y retrasos en la producción. Es importante realizar un análisis exhaustivo de cada paso y considerar la interacción entre ellos.
Ignorar factores externos
Otro error común es omitir los factores externos que pueden afectar el tiempo estándar de una actividad. Estos factores pueden incluir interrupciones, demoras en el suministro de materiales o cambios en las condiciones ambientales. Es esencial tener en cuenta estos elementos para obtener un cálculo preciso y evitar retrasos inesperados.
No utilizar datos históricos
Una práctica recomendada al calcular el tiempo estándar es utilizar datos históricos como referencia. Estos datos proporcionan información valiosa sobre el desempeño previo, permitiendo realizar estimaciones más realistas. No aprovechar este recurso puede resultar en una falta de precisión en el cálculo y una planificación deficiente.
No considerar la habilidad del trabajador
Cada trabajador tiene diferentes habilidades y niveles de experiencia. No tener en cuenta estas diferencias al calcular el tiempo estándar puede llevar a una sobreestimación o subestimación del tiempo requerido. Para obtener un cálculo preciso, es importante evaluar las capacidades individuales de los trabajadores y ajustar el tiempo estándar en consecuencia.
No actualizar regularmente los tiempos estándar
Los procesos y condiciones de trabajo pueden cambiar con el tiempo, lo que significa que los tiempos estándar también deben actualizarse periódicamente. No hacerlo puede llevar a una falta de precisión en la planificación y a resultados adversos en la producción. Es recomendable revisar y ajustar los tiempos estándar de manera regular para garantizar la eficiencia y calidad en el trabajo.
No considerar la retroalimentación de los trabajadores
Los trabajadores son quienes mejor conocen los detalles y desafíos de las tareas que realizan. No aprovechar su retroalimentación al calcular el tiempo estándar puede ser un error grave. La colaboración con el personal es fundamental para comprender las dificultades y ajustar el tiempo estándar según sea necesario. Esta retroalimentación puede brindar ideas valiosas para mejorar la calidad y eficiencia en el trabajo.
No contar con un margen de error
Por último, otro error común es no establecer un margen de error al calcular el tiempo estándar. Siempre existirá cierta variabilidad en los procesos y factores imprevistos pueden surgir durante la ejecución de una tarea. Establecer un margen de error adecuado permite adaptarse a estas situaciones y evitar retrasos significativos en la producción.
Evitar los errores comunes al calcular el tiempo estándar es fundamental para lograr una planificación precisa y eficiente en diversos sectores industriales. Teniendo en cuenta los consejos expertos presentados, podrás mejorar la precisión de tus estimaciones y maximizar la productividad en tu trabajo.
Cómo se puede establecer un sistema efectivo de registro y análisis del tiempo estándar en la producción
Establecer un sistema efectivo de registro y análisis del tiempo estándar en la producción es fundamental para optimizar los procesos y mejorar la eficiencia. El tiempo estándar se refiere al tiempo promedio que debería tomar completar una tarea o proceso específico. A través del cálculo del tiempo estándar, las empresas pueden determinar el rendimiento real y potencial de sus operaciones, identificar áreas de mejora y establecer metas realistas.
1. Definir las tareas y procesos
Antes de poder calcular el tiempo estándar, es necesario identificar y definir claramente las tareas y procesos involucrados en la producción. Esto implica desglosar cada actividad en pasos más pequeños y secuenciarlos correctamente. Es importante tener en cuenta todos los factores que puedan influir en el tiempo, como movimientos físicos, tiempos de preparación y tiempos de espera.
2. Recopilar datos
Una vez que se han definido las tareas y procesos, se deben recopilar datos sobre el tiempo requerido para completar cada uno de ellos. Esto puede incluir observación directa, registros de tiempo manuales o el uso de sistemas automatizados de recolección de datos. Para obtener resultados precisos, es recomendable realizar múltiples mediciones y promediarlas.
3. Calcular el tiempo promedio
Luego de recopilar los datos, es necesario calcular el tiempo promedio para cada tarea o proceso. Esto se puede hacer sumando los tiempos registrados y dividiéndolos entre el número total de mediciones realizadas. Es importante utilizar fórmulas o herramientas de cálculo adecuadas para evitar errores y obtener resultados precisos.
4. Aplicar factores de ajuste
En algunos casos, puede ser necesario aplicar factores de ajuste al tiempo promedio calculado. Estos factores tienen en cuenta variables como la fatiga del trabajador, las interrupciones inesperadas o los cambios en las condiciones de trabajo. Los factores de ajuste permiten estimar un tiempo estándar más realista que tenga en cuenta las circunstancias reales en las que se realiza el trabajo.
5. Monitorear y analizar continuamente
Una vez establecido el sistema de registro y análisis del tiempo estándar, es crucial monitorear y analizar continuamente los datos recopilados. Esto ayuda a identificar desviaciones, problemas recurrentes o áreas de mejora. La retroalimentación constante permite ajustar los tiempos estándar cuando sea necesario y mejorar la eficiencia general del proceso de producción.
Establecer un sistema efectivo de registro y análisis del tiempo estándar en la producción requiere una planificación adecuada, la recopilación precisa de datos y el análisis continuo. Al seguir estos consejos expertos, las empresas pueden calcular el tiempo estándar de manera rápida y precisa, lo que les permitirá optimizar sus procesos y alcanzar niveles más altos de eficiencia.
Qué consejos prácticos pueden ayudar a mejorar la precisión en el cálculo del tiempo estándar
Cuando se trata de calcular el tiempo estándar en una operación o proceso, la precisión es fundamental para obtener resultados fiables y realistas. Afortunadamente, existen varios consejos prácticos que pueden ayudarte a mejorar la precisión en este cálculo tan importante.
1. Define claramente la operación o proceso
Antes de comenzar a calcular el tiempo estándar, asegúrate de tener una comprensión clara de la operación o proceso que se va a medir. Esto implica conocer todos los pasos involucrados, las herramientas y materiales utilizados, así como también los posibles factores externos que podrían afectar la duración del proceso. Cuanta más información tengas, más preciso será tu cálculo del tiempo estándar.
2. Utiliza técnicas de medición adecuadas
Para calcular el tiempo estándar, es necesario realizar mediciones precisas de cada uno de los pasos o actividades que conforman la operación o proceso. Utiliza técnicas de medición adecuadas, como cronómetros digitales o dispositivos de conteo, para registrar con precisión los tiempos de cada actividad. Evita depender de estimaciones subjetivas, ya que esto puede llevar a errores significativos en el cálculo del tiempo estándar.
3. Considera el rendimiento del trabajador o máquina
Al calcular el tiempo estándar, es importante tener en cuenta el rendimiento esperado del trabajador o máquina que realiza la operación. Si se trata de un trabajador, evalúa su nivel de habilidad y experiencia en la tarea específica. Si se trata de una máquina, ten en cuenta su velocidad de funcionamiento nominal y cualquier tiempo de inactividad esperado, como cambios de herramientas o mantenimiento. Ajustar el cálculo del tiempo estándar para reflejar el rendimiento real te ayudará a obtener resultados más precisos.
4. Realiza mediciones repetidas
Para garantizar la precisión en el cálculo del tiempo estándar, es recomendable realizar mediciones repetidas de la misma operación o proceso. Esto ayudará a identificar posibles variabilidades o inconsistencias en los tiempos registrados, lo que permitirá obtener un promedio más preciso. Realizar mediciones repetidas también ayudará a detectar cualquier factor inusual o excepcional que pueda afectar la duración del proceso y ajustar en consecuencia el tiempo estándar.
5. Actualiza regularmente los tiempos estándar
Los procesos y operaciones están sujetos a cambios y mejoras con el tiempo. Por lo tanto, es importante actualizar regularmente los tiempos estándar para reflejar estos cambios. Revisar y ajustar los tiempos estándar periódicamente garantizará que los cálculos sean precisos y realistas, lo cual es fundamental para la planificación y gestión eficiente de los recursos.
Calcular el tiempo estándar de forma precisa es esencial para la eficiencia y productividad de las operaciones y procesos. Siguiendo estos consejos prácticos, podrás mejorar la precisión en este cálculo y obtener resultados confiables, lo que te permitirá tomar decisiones informadas y optimizar el rendimiento de tu organización.
Preguntas frecuentes (FAQ)
1. ¿Qué es el tiempo estándar?
El tiempo estándar es una medida de la cantidad de tiempo requerido para realizar una tarea o proceso en condiciones normales, sin ningún tipo de demoras o interrupciones.
2. ¿Cómo se calcula el tiempo estándar?
El tiempo estándar se calcula mediante la observación y medición directa de las actividades que componen una tarea, utilizando técnicas como el estudio de tiempos y movimientos.
3. ¿Cuál es la importancia del tiempo estándar?
El tiempo estándar es importante porque permite establecer metas realistas de producción, identificar y eliminar desperdicio de tiempo y recursos, y mejorar la eficiencia y productividad en los procesos.
4. ¿Cuáles son los factores que pueden afectar el tiempo estándar?
Algunos factores que pueden afectar el tiempo estándar incluyen la habilidad y experiencia del trabajador, las condiciones ambientales, la calidad de los materiales y herramientas utilizados, y la complejidad de la tarea.
5. ¿Cómo se puede reducir el tiempo estándar?
Para reducir el tiempo estándar se pueden implementar mejoras en los métodos de trabajo, utilizar tecnologías más eficientes, proporcionar capacitación y entrenamiento a los empleados, y fomentar la colaboración y el trabajo en equipo.
Deja una respuesta